يتم تصنيع أنابيب الإيبوكسي من خلال عملية لف الألياف الزجاجية حول قالب فولاذي في عملية تتم بدقة و بنمط حلزوني. هذه الأنابيب المركبة بقدراتها الفريدة تقدم حلًا هندسيًا للعملاء للكثير من التحديات في مختلف مراحل المشروع. تتمتع شركة صناعة الأنابيب المحدودة بميزة كبيرة تتمثل في امتلاكها القدرة على تصميم كافة الجوانب الهندسية المتعلقة بهذه الأنابيب. لذلك تتعامل الشركة مع كل مشروع بشكل خاص للتأكد من مطابقة كل التصاميم و المدخلات من ظروف و إشتراطات المشروع, علاوة على ذلك ، فإن هذه الميزة تتم بشكل موثوق و موثق من خلال تقديم مختلف المستندات الموضحه و الشارحة لجميع مراحل هذه المنتجات بدءا من إختيار المواد الخام مرورا بخطوات التصنيع و إنتهاء بتركيب و صيانة هذه المنتجات. كل هذه العمليات تتم إنطلاقا من خبرة سابقة تزيد عن 23 عامًا ، أنجزنا فيها أكثر من 3000 كيلومتر من الأنابيب وأكثر من 300000 قطعة مرفقة
الزجاجية الألياف أنابيب طبقات
الداخلي الطبقة
تعتبر هذه الطبقة على اتصال مباشر بالسائل المنقول في الأنبوب، لذلك يتم تصميمها لتضمن أقصى مقاومة للتفاعل الكيميائي الناتج من السائل. علاوة على ذلك ، تقدم هذه الطبقة سطحًا داخليًا ناعمًا بشكل خاص. حيث تتكون الطبقة من نسبة أقل من اللألياف الزجاجية مقارنة بكمية اللإيبوكسي
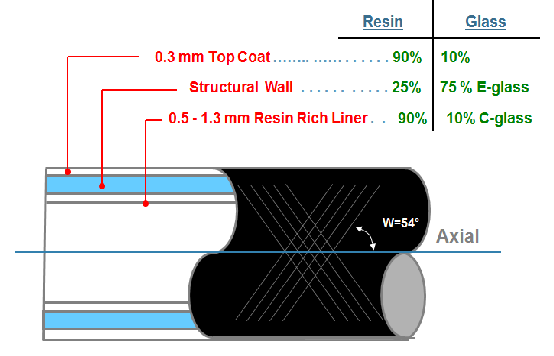
المتوسطة الطبقة
تتمثل وظيفتها في توفير مقاومة للضغوط بسبب ظروف التشغيل (الضغط الداخلي و / أو الخارجي ، وقوة الانحناء بسبب الأحمال الخارجية وما إلى ذلك). إذ يحدد سمك هذه الطبقة قوة و متانة الأنبوب
الخارجية الطبقة
غالبا تكون بسمك 0.3 مم وتتكون من مركب الإيبوكسي كمركب أساسي. تضمن هذه الطبقة حماية للطبقة المتوسطة و للألياف الزجاجية بها، وبالتالي يكون سطح الأنبوب الخارجي خاليًا تمامًا من الألياف البارزة مما يعطي الشكل المثالي للأنبوب . و يعتبر الهدف الرئيسي لهذه الطبقة هو توفير الحماية ضد الأشعة فوق البنفسجية الناتجة من أشعة الشمس