CPI supervisor Ensure compliance with Company’s HSE regulations while on site for installation, testing and commissioning of GRP piping system. They will perform Inspection of all GRP materials on site and report if any discrepancies are found. CPI supervisors shall also perform Inspection and ensure availability of proper equipment and other related GRP installation tools and materials, Ensure installation of pipe work in accordance with vendor’s specification and approved procedures. Identify any specialized enclosures / stops / ends required for field test. Check pipe work layout and supporting arrangements and make recommendations on any unforeseen problems regarding installation of the pipe. Supervise installation, handling and testing of the complete GRP pipe work, Witness hydro testing of the pipe system and verify that it is in accordance with the appropriate field test specification, Present and Ensure the correct alignment and make up of all flange connections, Sign all the joints records to confirm that the joints constructed are as per the approved procedure.
CPI bonders in lieu with supervision shall Ensure compliance with Company’s HSE regulations while on site for installation, testing and commissioning of GRP piping system, Ensure installation of pipe work in accordance with vendor’s specification and approved procedures, Report all defects of GRP product found during handling or installation, Any deviation to procedure or malfunction of tools and equipment during jointing work shall be identified to Company, Contractor and vendor representative.
Logistics, Handling And Shipping Procedure
All pipes and fittings ends shall be protected with end caps which can withstand long duration of storage and handling Pipes shall only be transported on trucks (side booms and other lifting equipment shall not be used to transport pipe on site for distances in excess of 50 meters) All chemicals and adhesives shall be transported in temperature controlled (200 C to 250 C) vehicles.
Trucks used to transport pipes shall be flat-bottomed and free of any projections or loose materials
Pipes shall be protected against truck beds and side metallic protrusions by means of non-metallic soft materials.
Support the pipe and spool layers on the wooden planks (4 Supports should be provided for each layer and should be located no more than 3 meter apart and up to 2 meter from the pipe ends).
The pipes shall be stacked to a height of 1.5 to 2 mtrs. Always place the wooden planks between layers. Pipes shall be stacked with bell ends in alternative directions
Secure the pipes with nylon slings (securing with metal rope or chains shall not be permitted) and lock them with wooden wedges.
Single pipes can be lifted with help of excavator mounted Vacuum lift of sufficient size and capacity.
Other than Vacuum lifting and Roller cradles, short pipe sections up to 6 m in length may be lifted with a crane using at least 100 mm wide canvas or nylon sling. Longer pipe sections may be lifted with a 6 mtr spreader bar and two 100 mm wide nylon slings. The lifting point or points shall be such that the pipes are well balanced.
Lifting of pipes at CPI yard shall be using fork lift.
Secure the pipes with nylon slings (securing with metal rope or chains shall not be permitted) and lock them with wooden wedges.
Single pipes can be lifted with help of excavator mounted Vacuum lift of sufficient size and capacity.
Other than Vacuum lifting and Roller cradles, short pipe sections up to 6 m in length may be lifted with a crane using at least 100 mm wide canvas or nylon sling. Longer pipe sections may be lifted with a 6 mtr spreader bar and two 100 mm wide nylon slings. The lifting point or points shall be such that the pipes are well balanced.
Lifting of pipes at CPI yard shall be using fork lift.
Small size Fittings shall be packed in a wooden box for transporting and site storage. Wooden pallets shall be used for larger fittings.
Installation contractor’s stores in charge shall ensure to keep the latest version of MSDS/SHOC cards for the chemicals stored at site.
Adhesive kits shall be stored in a controlled temperature of 20-25°C away from direct sunlight and excessive humidity (not more than 75%). A continuous record (Either chart recorder or Graph or Manual recording after every 1 hour) of temperatures of storage conditions shall be maintained. Same procedure should be followed during site works also i.e. during bonding activities the adhesive kits, which is sufficient for one day’s work shall be stored in a controlled temperature of 20 – 25°C.
The solvents used for cleaning must be stored separately with the statutory notices as these materials are highly inflammable.
The storage of the adhesive kit shall be in accordance with the Material Safety Data Sheet (MSDS). The MSDS will be sent from CPI along with the delivery of this material.
No consumable batch shall be stored or used beyond its stated shelf life.
Ancillary materials (Gaskets, centralisers, end seals etc), all equipment & tools (Heating blankets, Calibration machines, arbors, power drive, flapper wheel, grinder etc) shall be stored inside a lockable enclosure protecting them from sand, dust, humidity and direct sunlight
All rejected material shall be quarantined, packaged and transported to proper location as agreed with Company for disposal.
Machining procedure (for site)
Below Table shows the types of calibration machine to be used depending on the diameter :
Sl.No | Pipe Size | Type of Calibration Machine |
---|---|---|
1 | 15 - 80 | CPI M80 |
2 | 80-150 | CPI M86 |
3 | 150-400 | CPI M87 |
4 | 400 - 600 | CPI M87XL |
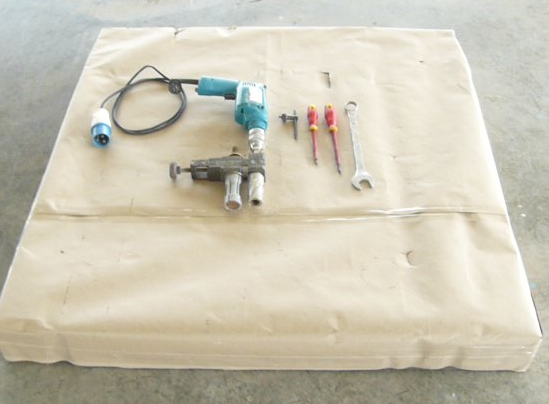
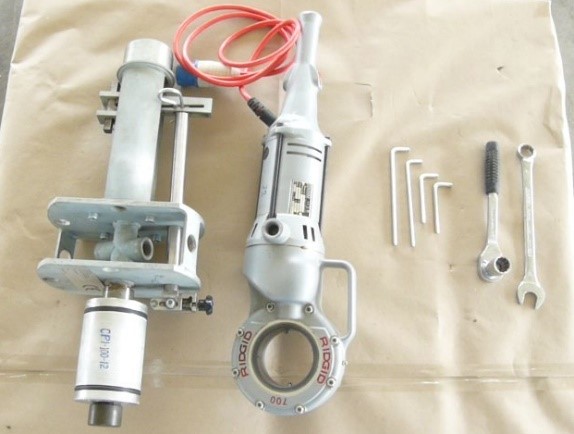
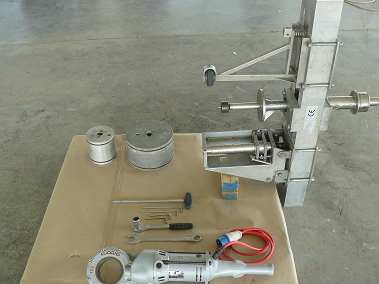
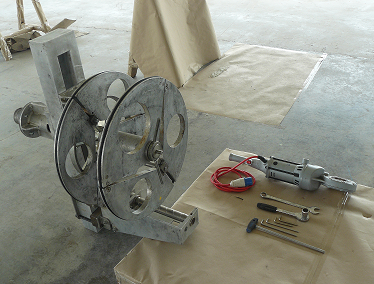
Adhesive Systems
Adhesive will be supplied in kits consists of two cans each (AV 4738 Epoxy Adhesive Resin and HV 4739 Epoxy Adhesive Hardener). Adhesive kits shall be stored in the original packaging in an air-conditioned environment with a controlled temperature between 20 to 25°C. Adhesives shall be used on a first in – first out basis.
The constituents of the adhesive shall be handled with care. It is recommended to wear gloves and goggles. The adhesive shall be prepared in a well-ventilated area.
In the event of adhesive contact with the skin, the affected area shall be washed with soap and water. In case, the adhesive enter into the eyes, immediately rinse thoroughly with water and refer to an eye specialist.
For more details refer the MSDS and technical data sheet supplied along with adhesive kits.
Note: Speed, Feed and depth of cut shall not create vibrations while calibrating the spigot.
Adhesive Mixing
Check the expiry of adhesive kit before use. Expired adhesive shall not be used. The complete hardener shall be removed from the can and added to the resin can. The entire resin and the hardener shall be mixed by spatula. Mixing shall continue until the adhesive mixture has a uniform and consistency colour. This shall be reached in the minimum possible time.(3 min)
The working pot life of the adhesive will depend on the surface temperature of the pipe at the time of bonding. For example if the pipe surface temperature is at 25°C, then the joint shall be assembled within 45minutes maximum. And if the pipe surface temperature is at 40°C, then the joint shall be assembled within 20 minutes maximum.
Bonding shall not be carried out when the bonding surface temperature is below 23°C or above 40°C prior to the application of the adhesive.
The exothermic reaction between the resin and hardener would start immediately after mixing, if the adhesive starts to heat up in the mixing can; it has started to get harden and must be discarded. If lumps or gels are apparent in the can, the adhesive must be discarded safely.
The table 2 below provide an approximate number of joints that can be done with one kit of 250 gms of adhesive.